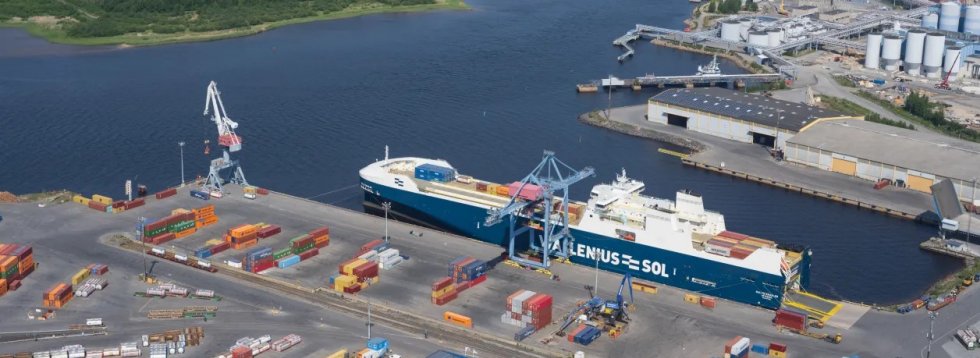
VTT, Oulu Port and Technology Firms in EUR 12.8 Million Project to Improve Security and Resilience in Ports
Feb. 10, 2025 - VTT Technical Research Centre of Finland and partners have launched a three-year project with Oulu Port aimed at enhancing secure situational awareness in critical cyber-physical systems. The complex structure of ports, with several operators and the challenges arising from this, underscores the importance of this initiative. Ports are critical nodes in transportation networks, making security a paramount concern. VTT and Oulu Port are collaborating with 20 other entities, including technology providers and universities, to improve the security and resilience in ports.
The total budget for the international research and development project is EUR 12.8 million. The project is funded by the participating organizations, foreign public research funders, and Business Finland. The project focuses on developing a secure situational awareness concept that enhances trust and security by building autonomous resilience into the system. This contributes towards ensuring that the port can recover from incidents and lower the risks for various digital and physical attacks.
Principal Scientist and project lead Juhani Latvakoski from VTT, points out, "In today's world, where hostile events are constantly unfolding, the emphasis on secure situational awareness has never been greater. Ensuring digital trust and security for the protection of critical cyber-physical systems, along with fostering situational awareness, appears to be an effective way to build resilience. The port serves as an excellent testing ground, mirroring a miniature society with its diverse and complex operations."
A key role in the project is played by the Port of Oulu, which is already at the forefront of digitizing port operations and has taken an active role in researching and applying the latest technical solutions. Situation and condition data from the port area is critical for the entire port ecosystem and its stakeholders.
The port is responsible for ensuring the safety and smooth flow of traffic in the area. Since 90% of Finland's exports pass through ports, the project is also important for the supply chains in Northern Finland.
Soila Riutta Development Manager at Oulu Port, explained, “We are developing a digital twin of the port area using various sensors, detectors, and radars. Additionally, innovative tracking and identification systems for port area traffic are of particular interest. New technologies provide opportunities, but a current challenge is that they primarily operate as separate applications. In this project, our goal is to create a comprehensive situational overview, particularly for managing safety and critical incidents.”
Ambitious Objectives and Targeted Benefits
The ambitious objective of the international R&D project led by VTT is to research and develop novel solutions enabling secure situational awareness that can be applied to improve security and resilience in various critical cyber-physical systems such as Oulu port.
“Unexpected events — such as accidents or physical and virtual attacks — can threaten the resilience of critical systems,” Latvakoski says. “These may result in blocked access to essential functions and resources, misuse of critical data, compromised physical safety, and lack of vital resources, which may cause fatalities, bankruptcies and even societal instability. Therefore, the project aims to develop secure situational awareness solutions, which are very important for critical logistics, mobility, energy, and security systems operating, e.g., in ports.”
The participating companies are conducting research and developing their own products and solutions, with the opportunity to pilot them and test their compatibility with other systems within the port area. The goal is to identify export-ready products and systems while enhancing collaboration between companies and supporting their international growth.
Riutta concludes, "The project is an important part of developing the port's security and resilience. We are excited to collaborate with leading technology providers to develop innovative solutions that will benefit all stakeholders."
VTT is one of Europe’s leading research institutions and is owned by the Finnish state. VTT advance the utilisation and commercialisation of research and technology in commerce and society.
SOURCE: VTT Technical Research Centre of Finland |
|
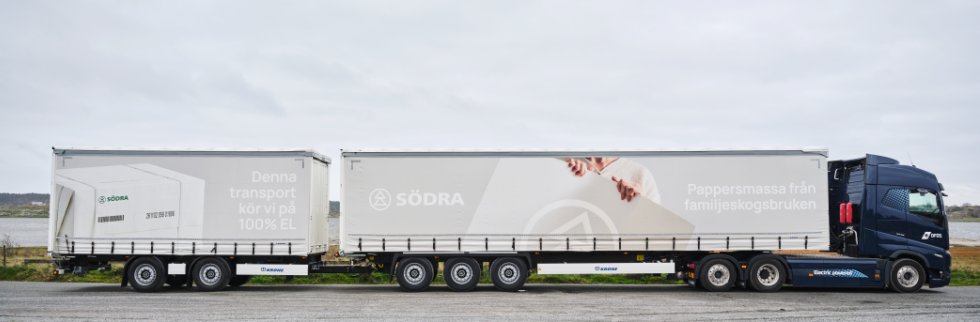
Södra Deploys First Electric Truck to Transport Pulp from Värö in Sweden
Nov. 28, 2024 - As part of its efforts to achieve its climate goal of net zero emissions of fossil greenhouse gases by 2040, Södra’s first electric truck is on the road. Part of a pilot project, the truck will be entirely dedicated to transporting fossil-free deliveries of pulp from Södra’s Värö mill to port terminals in Gothenburg and Varberg, Sweden.
The Värö mill produces softwood kraft pulp with a capacity of 760,000 tonnes per year. It is also a supplier of green energy, generating 1.6 TWh annually.
This month, some shipments of pulp from Värö will be delivered by electric truck as part of Södra's climate efforts to achieve net zero emissions of fossil greenhouse gases by 2040. This one truck is expected to save 48 tonnes of CO2 per year, compared with a diesel-powered truck.
Delivered by DFDS, the truck will transport pulp from Värö to port terminals in Gothenburg and Varberg during the pilot project. Each journey will have a load weight of 40 tonnes, which is the same volume as previous trucks using fossil fuel.
"The electrification of our transport is a natural part of our strategy to achieve our goal of net zero emissions of fossil greenhouse gases. It is also an important step in offering our customers more sustainable transport solutions and thus becoming a more attractive supplier. Several electrification projects are currently underway at Södra, and this pilot project to transport our pulp gives us valuable insight into where and how we can use electric trucks going forward," said Catrin Gustavsson, President of Södra Cell.
Södra's Path to Climate Neutrality
Södra strives to be a leader in society's journey towards climate neutrality. In this ambition, climate benefits will increase along the entire value chain — from family forestry to the products that are created from them.
To achieve its climate target, Södra is working to identify potential improvements in its operations and sees great opportunities in the electrification of machinery and transport. Södra currently has a positive energy balance and produced almost 2 TWh in 2023, creating opportunities for electrifying its vehicles.
Södra is now the largest forest-owner association with more than 50,000 family forest owners as members. Together, the members of Södra own a world-leading industrial operation that processes forest raw material into renewable products such as pulp, timber, building systems, liquid bioproducts and energy. In 2023, Södra generated sales of SEK 29 billion.
SOURCE: Södra |
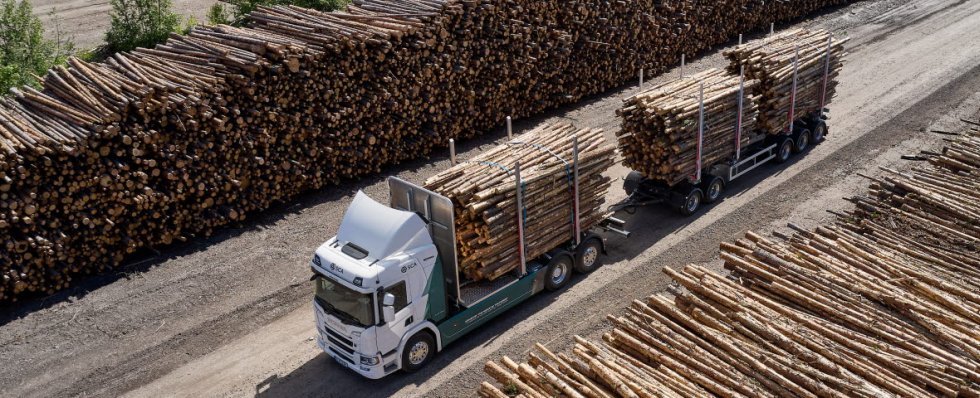
SCA's Electric Timber Truck from Scania Is Now in Operation
July 6, 2022 - SCA, together with Scania, has developed the world's first electric timber truck with a capacity to carry 80 tonnes and the new truck has been delivered to SCA.
“We have come a long way in the industrial processes that are already today 96 percent fossil-free,” said Hans Djurberg, head of sustainability at SCA. “We are very happy to be able to break new ground together with Scania to make the heaviest transports fossil-free.”
Fredrik Allard, head of E-mobility at Scania, explained, “The 80-ton battery-powered timber truck shows that even really heavy transports can be electrified. The partnership with SCA — where you are out early and show what is possible — is a clear signal that it is possible to electrify even heavy transports.
“An electric timber truck is a symbol of something quite cool. Shipping of just timber has been talked about as something that might never be possible to electrify. The development in recent years and what we now present together with SCA shows how fast the development takes place both in terms of vehicles and batteries,” Allard added.
Test Runs During the Summer
SCA said the intention is for the vehicle to transport timber on the stretch between SCA's timber terminal in Gimonäs and the paper mill in Obbola outside Umeå. The new electric timber truck is another innovative step on the journey towards a fossil-free society and can be driven with a total weight of 64 tonnes on public roads and 80 tonnes on private roads.
The electric timber truck will be tested during the summer and continuously studied by the research institute Skogforsk to collect relevant data that can form the basis for comparisons with conventional diesel-powered timber transports. Thereafter, the plan is for it to be included in SCA's regular operations.
Djurberg noted, “This is a first concrete step towards electric power in the most difficult part of the land-based transport chain, which is extremely important. This is a global challenge that many have struggled with and now we are showing together with an innovative partner, Scania, that Swedish industry can drive sustainability development.
“The studies carried out during the summer will, among other things, compare energy consumption, productivity and costs in relation to existing vehicles and map out what would be required for a broad implementation of electric timber trucks throughout the country.”
Trial Facts
- 6 turns per day, Gimonäs timber terminal to Obbola paper mill, Monday-Friday, approx. 07: 00-17: 00.
- Distance: about 30 km round trip
- Time required: approx. 75 min per load (including loading / unloading)
- The car is charged with an ABB charger of 180 Kw at Obbola.
According to SCA, a single electric truck used between Gimonäs and Obbola means that SCA can reduce emissions by about 55,000 kg of carbon dioxide per year.
The project is part of REEL, a national initiative where leading Swedish players have joined forces to accelerate the transition to electrified emission-free heavy transport on our roads. The initiative, led by CLOSER, is part-financed by the Vehicle Strategic Research and Innovation (FFI) program through Vinnova and the Swedish Energy Agency.
SOURCE: SCA |
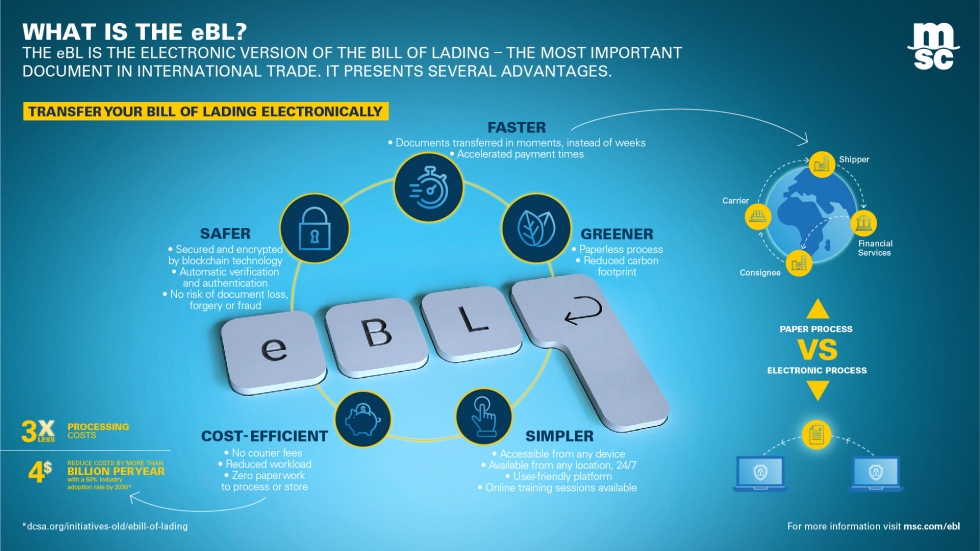
MSC Introduces New Electronic Bill Of Lading for Customers Worldwide Using Wave BL’s Platform
April 28, 2021 - MSC Mediterranean Shipping Company, a global leader in container shipping and logistics, is officially introducing the electronic bill of lading (eBL) for its customers around the world, following a successful pilot phase, using a solution on an independent blockchain platform WAVE BL. The eBL enables shippers and other key supply chain stakeholders to receive and transmit the bill of lading document electronically, without any change or disruption to day-to-day business operations.
WAVE BL is a blockchain-based system that uses distributed ledger technology to ensure that all parties involved in a cargo shipment booking can issue, transfer, endorse and manage documents through a secure, decentralised network. Users can issue all originals, negotiable or non-negotiable, and exchange them via a direct, encrypted, peer-to-peer transmission. It’s also possible for users to amend documents. WAVE BL’s communication protocol is approved by the International Group of Protection & Indemnity Clubs, and meets the highest industry standards for security and privacy.
“MSC has chosen WAVE BL because it is the only solution that mirrors the traditional paper-based process that the shipping and cargo transportation industry is used to,” says André Simha, Global Chief Digital & Information Officer at MSC. “It provides a digital alternative to all the possibilities available with traditional print documents, just much faster and more secure.”
The WAVE BL platform can be used free of charge throughout 2021 for exporters, importers and traders. Users only pay for issuing the original documents, and they do not need to invest in any IT infrastructure or make operational changes in order to use the service. They can simply sign up via MSC’s website: www.msc.com/eBL.
MSC Mediterranean Shipping Company, headquartered in Geneva, Switzerland, is a global leader in transportation and logistics, privately owned and founded in 1970 by Gianluigi Aponte. As one of the world’s leading container shipping lines, MSC has 524 offices across 155 countries worldwide with over 100,000 employees. With access to an integrated network of road, rail and sea transport resources which stretches across the globe, the company prides itself on delivering global service with local knowledge. MSC’s shipping line sails on more than 215 trade routes, calling at over 500 ports.
SOURCE: MSC |
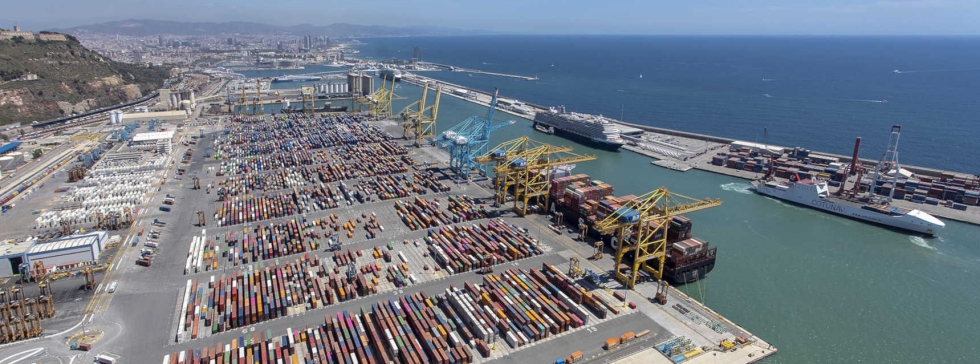
APM Terminals Barcelona Applies 5G Technology to Improve Traffic Safety
The system is based on the application of connected car technology and industrial traffic safety. The information will be shared continuously and offer the position and trajectory of machinery, vehicles, and people in real time, enabling traffic coordination and warning drivers in the event of an accident risk.
March 11, 2021 - 5G Barcelona, together with Telefónica, APM Terminals, and Mobile World Capital Barcelona are working on a pilot project to improve security in ports thanks to the use of 5G networks to connect cranes, vehicles, and people by merging different advanced communication and localisation technologies. The main objective of the project is to minimise the potential risk of collisions between mobile machinery and fixed elements, vehicles, and people in the container terminal.
5G Barcelona is a public-private initiative that works to position Barcelona and Catalonia as an innovative and open environment for the validation and adoption of 5G technologies and applications in a real-life environment.
The pilot test, which is based on technology of the C-V2X connected car and the low latency of 5G communications and Edge Computing, aims to turn APM Terminals Barcelona into a safer space for workers, thanks to a system that allows the coordination of port traffic and the implementation of advanced algorithms for accident traffic prevention. Through an alarm system, both crane drivers and trucks or pedestrian personnel will be warned about a potential collision against fixed and mobile elements and the system will in addition send an instant notification to a control centre in case of collision.
The development of the project involves the deployment of Telefónica's 5G coverage at the APM Terminals in the Port of Barcelona, the provision of 5G connectivity to Straddle Carrier cranes, trucks and terminal personnel, as well as an acoustic warning system for possible collisions.
“Transition towards a fleet of natively connected vehicles”
The Straddle Carrier cranes will be equipped with an on-board unit capable of communicating via 5G and through C-V2X technology between them and with the rest of the actors. Trucks, truckers and terminal personnel will have a 5G smartphone, on which a C-V2X application will be installed. This way, the smartphone, becomes another piece of the V2X environment, as well as the lever for an easy transition towards a fleet of natively connected vehicles and direct inclusion of people in the ecosystem.
Fixed elements, such as streetlights, will also be signalled with C-V2X communications, thus communicating with the rest of the mobile actors in real time.
All the information communicated by the cranes, trucks and pedestrian personnel is sent securely to an application located geographically very close (Edge) to their place of consumption in order to offer immediate responses. This application, hosted on the Edge, has the intelligence to be able to coordinate this cooperative driving between the different actors — called intelligent cooperative transport system (C-ITS) — and also offers a dashboard to APM Terminals to visualise on a map the positions of each of the actors participating in the project. Obtaining a precise location is vital and for this reason a system has been developed to allow obtaining precise locations as close as centimetres.
APM Terminals operates one of the world’s most comprehensive port networks with 75 terminals. To learn more, visit: www.apmterminals.com. |
|
|